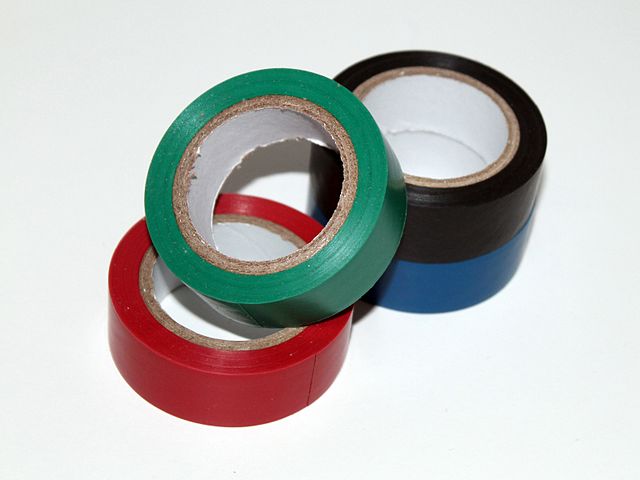
Min ståndpunkt har alltid varit att alla kan ägna sig åt förbättringsarbete som att skapa en 5S-standard på en arbetsstation. Antingen är jag för naiv, eller så krävs det en kurs, åtminstone intern, för att lära folk syftet med 5S.
En kollega, på en annan avdelning, på min tidigare arbetsplats, missförstod syftet med 5S på ett djupare plan. Troligtvis på grund av att denne dels saknade förståelse, vilket ledde till att personen förlöjligade 5S och satte etikett på linjaler, hålslag och fläktar. Etiketter med sakens namn.
Missförstå mig inte, det är inga problem att märka upp vissa arbetsredskap och maskiner med namn. Men då handlar det i första hand om ovanliga saker som exempelvis vattenavskiljare, något som kan hjälpa personer vid felsökning. Att däremot märka upp en bordsfläkt med namnet fläkt och linjal med ”linjal går till överdrift.
Vad man däremot bör göra är att markera upp ett område på bordet där fläkten, hålslaget och linjalen skall placeras och där märka upp en ruta med tejp och etikett. Då har man en specifik plats för sakerna.
Tyvärr har inte alla kunskap om övriga steg i 5S-arbetet utan tror att ett par meter tejp och etiketter skapar ordning och reda. Absolut, var sak på sin plats är en viktig del, men man har då missat övriga steg i processen.
Som ni vet handlar det om att sortera vilka saker som är nödvändiga för arbetet, och vad som kan avlägsnas. Förutom att märka upp arbetsplatsen handlar strukturera även om att placera verktyg och utrustning på ett så bra ställe som möjligt så att man maximerar den värdeskapande tiden. Självklart behöver man städa arbetsplatsen och dessutom komma fram till en standard, och dokumentera denna, där man beskriver hur arbetsplatsen skall se ut varje dag.
Vi har på min arbetsplats fått i uppdrag att märka upp avställningsytor, golv och lagerplatser i produktion. Det har absolut blivit bättre än tidigare, men eftersom att vi är flera som arbetat med det, till stor del utan konkret plan, så har jag märkt att en del uppmärkta platser inte alls är placerade på den mest optimala platsen, det gäller även om det enbart är tejp på en bordsyta.
Frågan är hur man bäst lär ut 5S så att hela organisationen, från ledningsgrupp till produktionspersonal, får förståelse om varför det är så viktigt med struktur, vad man bör tänka på och hur man skall arbeta. Det kanske bör bli mitt nästa projekt?